Over the past 30 years of reform and opening up, China's economy has experienced rapid growth. We have become accustomed to speed and find it hard to tolerate delays. Phrases like "Bai Qigong in a battle" often reflect the high-stakes nature of business decisions. Companies tend to favor quick wins, but this fast-paced mindset often leads to superficial innovation. To truly advance, enterprises must shift their thinking, overcome impatience, and focus on foundational work.
**Shimaru Yuji, President of the Japan Machine Tool Manufacturers Association:**
Japan's machine tool industry ranks second globally in production value, with 70% of its output exported. As markets become more globalized, customer demands for functionality, performance, and cost efficiency are increasing. To meet these diverse needs and foster long-term relationships, we must continue to deliver high-quality machine tools. This requires a clear understanding of our position in the global market and a well-defined vision for future development.
**Yuan Li, Chief Engineer of Shenyang Aircraft Industry (Group) Co., Ltd.:**
The cross-generation development of aircraft and the surge in demand pose significant challenges for manufacturing. New materials, structures, and processes are constantly emerging, making traditional equipment insufficient. It is now urgent to adopt advanced machinery to address bottlenecks in key aircraft component production.
**Liu Shulin, Director of the Center for Technology Innovation and Strategic Management, University of Chinese Academy of Sciences:**
While China’s economy has grown rapidly over the past two decades, most enterprises still rely on incremental or secondary innovation. Many core technologies remain unresolved. To achieve breakthrough innovation, companies need to invest in basic research, build strong innovation platforms, and create environments that encourage creativity. This includes rethinking education systems and innovation ecosystems to support sustainable industrial transformation.
**Enrico Anacondia, Consultant of the Italian Machine Tool, Robotics and Automation Manufacturers Association:**
Machine tool design and application are moving toward more sustainable directions, with higher performance expectations. End-user demands and regulatory standards are increasing, making safety, reliability, and repeatability essential. The Italian industry is developing new technologies to support sustainable growth across different sectors.
—Excerpted from experts at the high-level international forum “Innovation · Sustainable Developmentâ€
In 2012, China’s machine tool industry faced a downturn, marked by declining total output, sales, and profits. Despite this, key enterprises saw 22 consecutive months of rising orders. However, many domestic exhibitors admitted that reduced market demand has created unprecedented pressure.
**Why foreign machine tools are gaining ground**
In 2012, domestic machine tool sales fell by 17.9%, while imports rose by 6.03%. Domestic market share for metal cutting machines dropped by 1.8 percentage points, and CNC machine tools lost 1 percentage point. This trend highlights the growing preference for foreign brands.
**Why foreign brands dominate the Chinese market**
Wu Bolin, executive vice president of the China Machine Tool Industry Association, noted that China’s low-end capacity is excessive, while high-end capabilities are lacking. As industries upgrade, demand for better quality machine tools increases. For example, in the automotive sector, high-end vehicles require precision manufacturing, which domestic tools often fail to deliver. Hence, companies turn to foreign suppliers.
Some Chinese high-end machine tools may look similar to foreign ones, but quality differences are evident. Issues like inefficiency, instability, and declining accuracy over time make them less attractive. As one insider said, “Domestic companies prefer foreign products.â€
**Improving high-end competitiveness is urgent**
Wu Bolin emphasized that China’s machine tool industry is still at the lower end compared to developed nations. While the market has grown rapidly, many companies neglected technological innovation. Now, with changing market dynamics, transformation and upgrading are essential.
Chen Huiren, deputy secretary general of the association, stated that future growth must rely on technology, management improvements, and skilled labor. The key task is to enhance the competitiveness of high-end machine tools, as low-end products are no longer sufficient.
Several companies have adjusted their strategies, reducing low-end offerings and expanding medium- and high-end production. Technological innovation is critical in improving product quality, service, and efficiency.
**Innovation driven by speed is often not effective**
Wang Bin, deputy general manager of China General Technology (Group), pointed out that the real issue behind poor competitiveness is the lack of comprehensive enterprise quality. Companies need stronger market-oriented strategies, innovation mechanisms, and operational management.
Guan Xiyou of Shenyang Machine Tool Group highlighted the need for transformation, shifting from manufacturers to service providers. At the exhibition, Shenyang Machine Tool introduced advanced CNC machines like I5, BRIO, and SMART, integrating smart technology and improved service concepts.
As one executive noted, “Innovation is important, but so is business philosophy. Both must be implemented through people.†German and Japanese companies emphasize long-term dedication and quality, offering lessons for Chinese firms.
Finally, Chen Huiren concluded: “Over the past 30 years, we have become used to speed. But this fast mentality often leads to shallow innovation. Enterprises must change their mindset, overcome impatience, and focus on solid, fundamental work.â€

Wind Energy Fasteners Supplier China, Yokelink
sales@yokelink.com
Yokelink has been supplying fasteners for the wind energy industry for over 10 years. These fasteners are utilised in producing a gearbox, a valuable wind mill turbine component located within the nacelle. we also offer standard wind power energy fasteners in line with ISO or DIN, including vibration-resistant security products. Wind tower bolt plays a important role as joining components in fastening different parts of wind turbine tower, Yokelink is a professional manufacturer which supplies high grades fasteners 8.8-12.9 for wind tower projects.
Product Ranges:
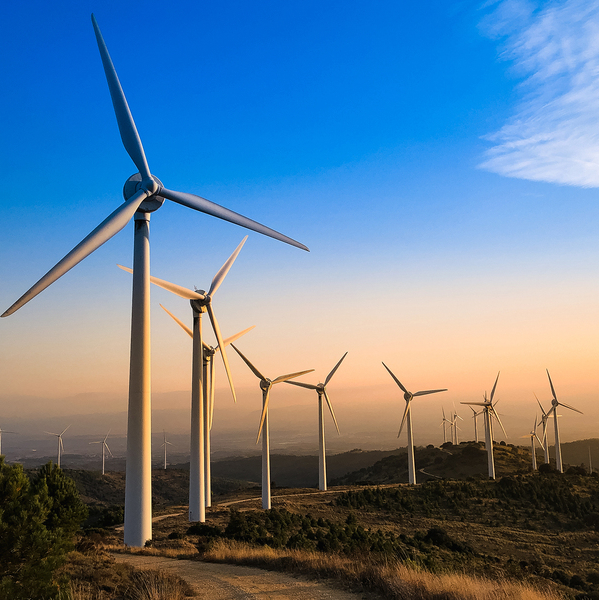
We currently service all aspects of the wind turbine market, Our extensive range allows wind
turbine manufacturers to 'single source'all their fastener requirements with all the advantages that this brings, providing a range of fasteners, both standard and customer bespoke for:
turbine manufacturers to 'single source'all their fastener requirements with all the advantages that this brings, providing a range of fasteners, both standard and customer bespoke for:
â—Foundation
â—Tower Construction
â—Blade to Hub
â—Nacelles
â—Off-shore Transition Pieces
Hex cap screws DIN 931, DIN 933 and ISO 4017
Hex Bolts and Nuts, size M10-M64
Stud Bolts size M12-M64
Threaded Rods size M10-M64
Tower Flange Bolts size M10-M64
WHAT ARE WINDMILL POWER FASTENERS?
WHAT ARE WINDMILL POWER FASTENERS?
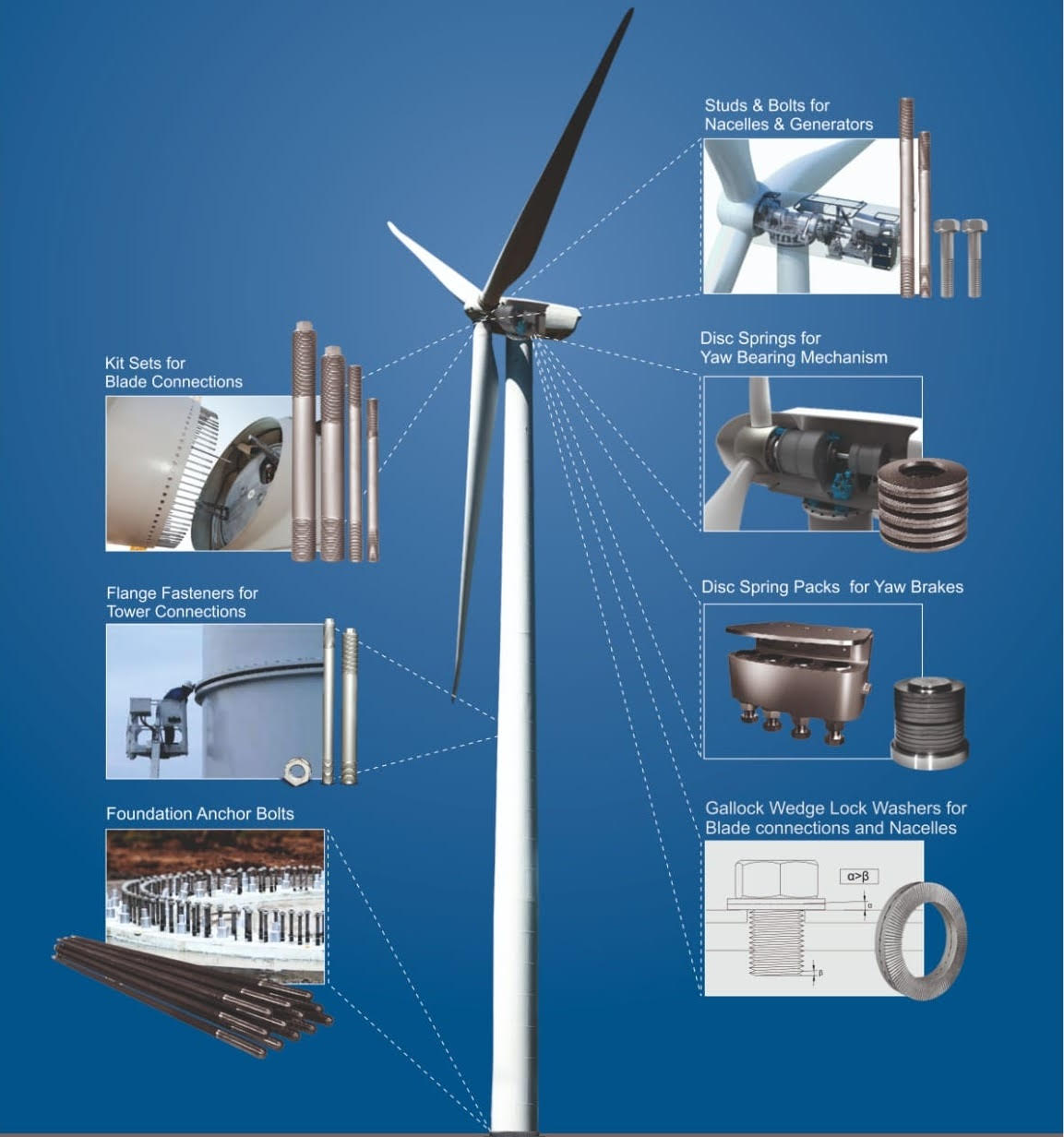
Fasteners used in wind power tower and blade connection and transmission, including hex bolts, stud bolts, tower flange bolts, foundation bolts, threaded rods, high strength double head screw, hardened and structural bolts, nuts, washers and threaded rods, and hex cap screws etc.
WHAT'S THE CHARACTERISTICS OF WIND POWER FASTENERS
High strength, high grade and precision, can work in hard conditions like extremely hot and cold environment and corrosion resisted .In wind turbine generator system, because of the randomness of power source, hardness of operating circumstances, special producing and installing, as well as high costs of maintaining, the requirements for wind turbine bolts would be extremely high. We have to take effective actions to ensure the reliability of the bolts connection, from the bolts structure design, manufacture process to production and assembling.
WHAT BOLTS ARE USED IN A WIND TURBINE?
Wind turbine bolts, there are wind turbine blade bolts, wind turbine anchor bolts, wind turbine foundation bolts, high strength and high tension hexagon head bolts, nuts and washers are mainly used for wind turbine.
HOW MANY BOLTS ARE IN A WIND TURBINE?
A most common 3 blades wind turbine requires almost 25,000pcs fasteners. With the rapid increase of wind energy demand in the worldwide, the fasteners for wind turbine and energy increased greatly as well. Most high strength bolts used for wind turbine are grade 10.8, grade 12.9 and the coatings are also very crucial, Dacromet are most commonly coating in wind turbine fasteners.
A most common 3 blades wind turbine requires almost 25,000pcs fasteners. With the rapid increase of wind energy demand in the worldwide, the fasteners for wind turbine and energy increased greatly as well. Most high strength bolts used for wind turbine are grade 10.8, grade 12.9 and the coatings are also very crucial, Dacromet are most commonly coating in wind turbine fasteners.

When you need Wind Power Fasteners, refer to above our catalog. We offer them in a full selection of sizes, provide the diameter or part number to get a quote of wind power fasteners, leave your message, or send us an email. You can also call us to get answers to your questions and place your order.
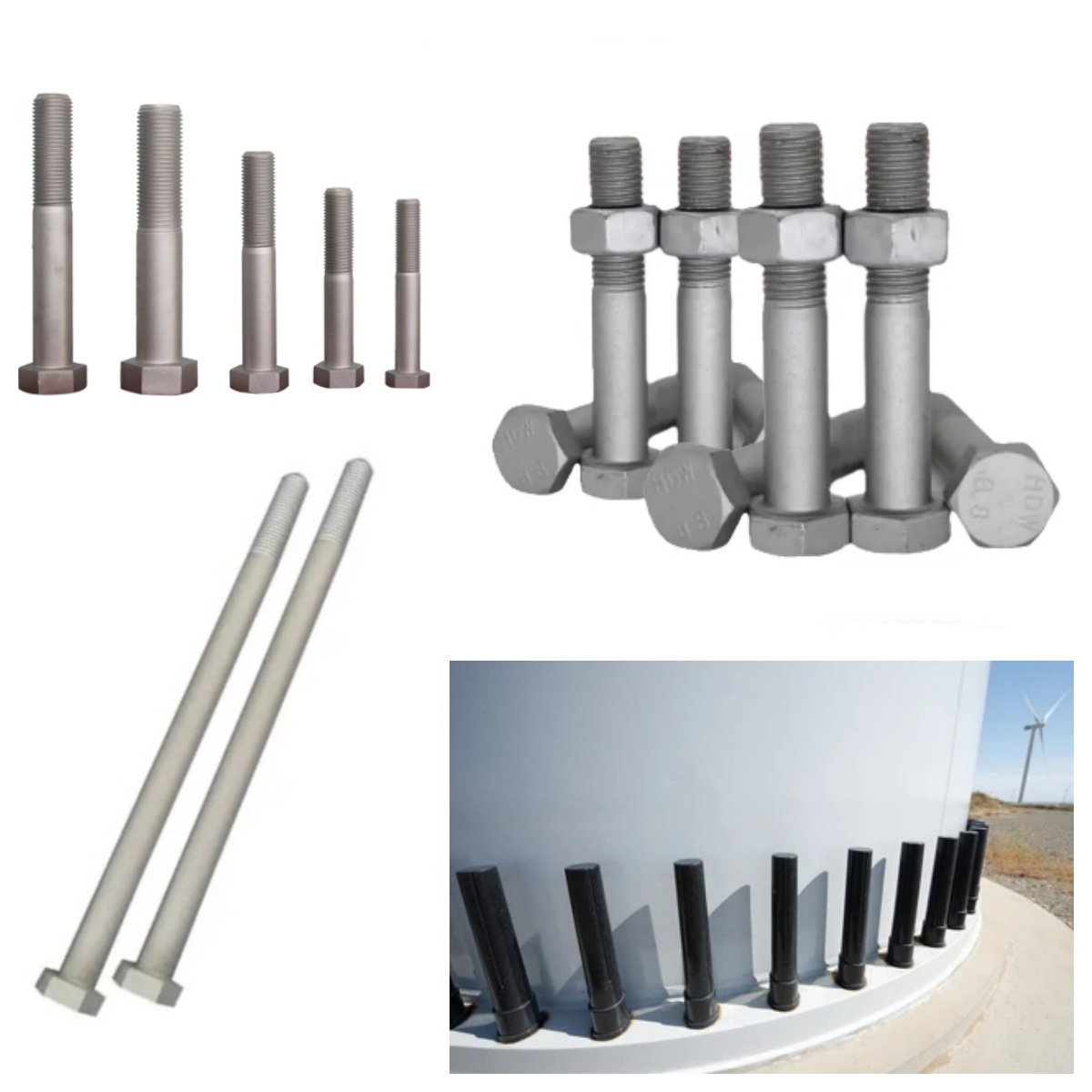
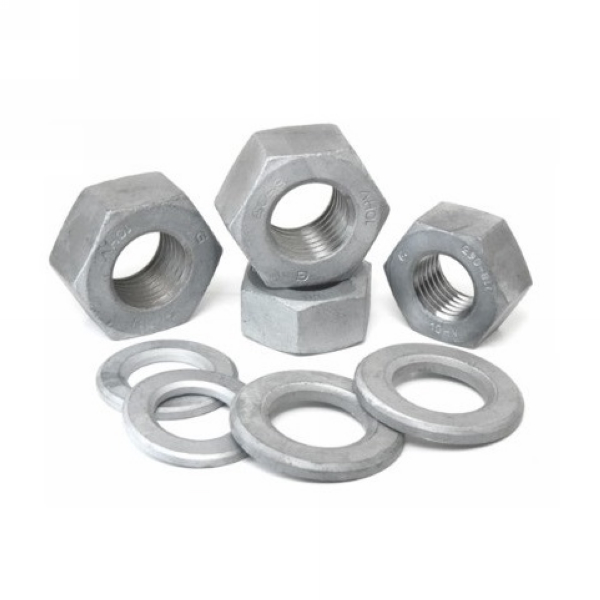

Wind Energy Fasteners Supplier China, Yokelink
sales@yokelink.com
Wind mill ,Wind Power fasteners, Wind mill Turbine, Stud Bolt, windmill energy, house wind turbine, Wind Turbine Blades
Ningbo Yokelink Machinery Co.,Limited , https://www.yokelink.com