Abstract: This paper introduces the types, development process, manufacturing methods, performance and application range of superhard tool materials (diamond and cubic boron nitride), and includes some test data for cutting difficult materials.
Key words: superhard material; diamond; cubic boron nitride; tool; cutting performance
1 Introduction
Modern tool materials The main hard components of high-speed steel, cemented carbide and ceramics are carbides, nitrides and oxides. For example, high speed steel is iron carbide added with alloying components (W, Mo, etc.); hard alloys are mainly carbides, nitrides and carbonitrides: ceramics are oxides and nitrides. These compounds have a hardness of up to 3000 HV and a bonding material with an overall hardness of less than 2000 HV. For the processing of modern engineering materials, in some cases, the hardness of the above-mentioned tool materials is no longer sufficient, so super-hard tool materials came into being, and there was a great development in the last 40 years of the 20th century. The chemical composition of superhard materials and the hardness of their formation are different from those of other tool materials. Cubic boron nitride is a non-metallic boride with a crystal structure of face-centered cubes; while diamond is converted from carbon, its crystal structure and cubic nitrogen Boron is similar. Their hardness is much higher than other substances.
Human diamonds have been discovered and used thousands of years ago; the manufacture and application of synthetic diamonds was a thing of the last century. Boron nitride is artificial. In the late 20th century, two kinds of superhard materials such as synthetic diamond and cubic boron nitride were developed.
Synthetic diamonds have been formed under high temperature and high pressure (hot pressing) conditions, called PCD, and other manufacturing methods have appeared. The research on PCD synthetic diamond began in 1940. In 1954, the United States officially announced the successful development of such diamonds, and industrial production began in 1957. Sweden declared success in 1953 and industrial production began in 1962. By 1969, the world's synthetic diamond production was 40 million carats; the annual natural diamond production was 44 million carats. In 1963, China announced the success of PCD manufacturing. In 1996, China's synthetic diamond production reached 240 million carats and exported 6 to 8.5 million carats. At the end of the 1990s, China's annual output reached 500 million carats, ranking first in the world. The largest foreign company with an annual output of synthetic diamond has reached more than 100 million carats in recent years.
In 1957, GE Corporation of the United States pressed out CBN (cubic boron nitride) single crystal powder, and in the early 1970s, it made polycrystalline PCBN cutter. In 1972, the Soviet Union also made PCBN tools. In 1966, China successfully developed single crystal CBN. Later, PCBN is made.
In recent years, synthetic diamond has been produced by chemical vapor deposition (CVD).
2 Types of superhard tool materials
Superhard tool materials, especially diamonds, come in many varieties.
Cubic boron nitride has CBN single product powder for making abrasive tools; PCBN poly wafers and PCBN polycrystalline composite sheets for making tools and other tools. Cubic boron nitride is man-made.
Diamond is divided into natural diamond (ND) and synthetic diamond. Synthetic diamond has PCD single crystal powder for making abrasive tools; PCD single crystal can be used as tool; PCD poly wafer and polycrystalline composite sheet for making tools and other tools; CVD diamond film and thick film can be used for making Tools, tools, and high-tech raw materials for optics and electronics.
3 Superhard tool material manufacturing method
There are many manufacturing methods for artificial superhard tool materials. The hot pressing method and vapor deposition method are mainly introduced here.
The equipment used to make diamond and cubic boron nitride by hot pressing is a six-sided top or two-sided hydraulic press. Pressing single crystal superhard material. The material needs to be placed in the cavity of the pyrophyllite. The raw material for pressing the PCD single crystal powder is graphite sheet, and the graphite sheet and the catalyst Ni-Mn sheet are stacked in the cavity; the raw material for pressing the PCD poly wafer is PCD single crystal powder, and the bonding agent Ni, Si, Co, etc. is added; The raw material of the CBN single crystal powder is hexagonal boron nitride (HBN) powder; the raw material for pressing the PCBN poly wafer is CBN single crystal powder, and the catalyst and the binder are separately disposed. The hot pressing process is shown in Figure 1 and Figure 2. The pressure, temperature and pressurization time are listed in the figure.
The pressure during pressurization is different from the pressure rise and final pressure. The pressure in the pyrophyllite cavity is different from the pressure in the top hammer. The pressure shown in Figure 1 and Figure 2 refers to the pressure in the top hammer. . The temperature is the cavity temperature. Time is the sum of the heating time, holding time and cooling time. These parameters will be different for various presses. The data given in this paper is only a rough figure.
PCD is produced by a similar hot pressing method, and there is also an "explosion method" in which a high temperature and a high pressure are generated by explosion of an explosive in a container to convert graphite into diamond. The process and product quality of the explosion method are not easy to control, so it is rarely used officially.
The CVD method is a vapor deposition method. There are many methods for depositing diamond on a non-diamond substrate, such as "hot wire CVD method", "electron reinforced CVD method", "microwave PCVD method", "radio frequency PCVD method", "direct current PCVD method", "DC arc PCVD method", "DC plasma jet CVD method", "electron cyclotron resonance PCVD method", "flame combustion method", "excimer laser CVD method", and the like. The "hot filament CVD method" is most commonly used.
Figure 3 is a schematic diagram of the principle of hot wire CVD diamond thick film growth deposition technology. The raw materials are ethanol (alcohol), hydrogen and methane, and the hot wire is Ta or W wire. The hot wire heated to a high temperature of 2000 to 2500 ° C and a plasma formed by applying a voltage between the hot wire and the substrate dissociate the hydrogen molecules from the carbon-containing gas molecules to form atomic hydrogen and a hydrocarbon group capable of forming an SP 3 bond. The group undergoes a chemical process of adsorption at the surface of the substrate at an appropriate temperature under the action of atomic hydrogen to dehydrogenate to form a carbon structure of the diamond. Controlling the temperature of the hot wire and applying the voltage and current density, particularly the composition of the gas, the pressure of the growth vessel, and the temperature of the substrate, can effectively control the rate of film growth and the quality of film formation.
After forming a thick film on the substrate (substrate), the film is separated from the substrate and cut into small pieces of a certain shape, and the small pieces are brazed on the cemented carbide to form a composite blade or a cutter, as shown in FIG. .
If a CVD thin film diamond tool is manufactured, the diamond film can be directly deposited on the tool, and the film thickness is only about 10 μm. The thickness of the thick film can reach 0.5 to 0.6 mm or more.
4 performance of superhard tool materials
Superhard materials have excellent mechanical, physical and other properties, some of which are well suited for tools.
4.1 has a high hardness
Natural diamond has a hardness of 10,000 HV; CBN has a hardness of 7500 HV. Compared with other hard materials, SiC hardness is 3000~3500HV, A12O3 is 2700HV, TiC is 2900~3200HV, WC is 2000HV, Si3N4 is 2700~3200HV, and hard alloy used as tool material has hardness of only 1100~1800HV. .
4.2 has good thermal conductivity
The thermal conductivity of human diamond reaches 2000W?m-1?K-1, and the thermal conductivity of CBN reaches 1300W?m-1?K-1. The thermal conductivity of copper is very good, its thermal conductivity is only 393W?m-1?K-1; pure aluminum is 226W?m-1?K-1, so the thermal conductivity of diamond and CBN is 5 times that of copper respectively. And 3.5 times, 8 times and 5 times that of pure aluminum. The thermal conductivity of cemented carbide is only 35-75W?m-1?K-1.
4.3 has a high Young's modulus
The Young's modulus of natural diamond is 1000 GPa, and the Young's modulus of CBN is 720 GPa. The Young's modulus of SiC, Al2O3, WC, and TiC is only 390, 350, 650, and 330 GPa, respectively. The large Young's modulus of matter is good rigidity.
4.4 has a small thermal expansion
The linear expansion coefficient of natural diamond is 1×10-6/K, and the linear expansion coefficient of CBN is (2.1 to 2.3)×10-6/K. The coefficient of linear expansion of cemented carbide is (5-7)×10-6/K.
4.5 with a lower density
The natural diamond has a density of 3.52 g/cm3 and the CBN has a density of 3.48 g/cm3. It is close to the density of Al2O3 and Si3N4.
4.6 has low fracture toughness
The fracture toughness of natural diamond is 3.4 MPa?m0.5, and CBN is close to it. The fracture toughness of ceramic tool materials is lower among various tool materials, but it can still reach 7 to 9 MPa?m0.5. Therefore, diamond and CBN are brittle and are weak points.
4.7 Chemical properties
CBN has good thermal stability and does not decompose in the atmosphere at 1300-1500 °C. It is inert to iron-based elements; it is not eroded in acid, and is etched at about 300 ° C in alkali; it also works with superheated water vapor. The diamond is chemically stable at normal temperature; graphitization starts at about 660 ° C in oxygen, and iron group elements, especially iron elements, can promote graphitization; they are not etched in acid or alkali.
4.8 Electrical properties
Pure, impurity-free diamond is an insulator with a resistivity of 1016 Ω·cm or more at room temperature. Semiconductor properties are exhibited only after the addition of other elements. Compared with semiconductor materials such as Si, Ce, and As, diamond has a very wide forbidden band, a small dielectric constant, a high electron carrying mobility, and a large electrical breakdown strength, indicating that diamond is an excellent ban. With high temperature (>500 ° C) semiconductor materials. Natural diamond is non-magnetic; if synthetic diamond contains catalytic impurities such as Ni, Co, Fe, etc., it has magnetic properties, and the more impurities, the stronger the magnetic properties.
4.9 Optical properties
Diamond has a high refractive index and strong astigmatism, and also has excellent light transmission properties, which can penetrate a wide range of wavelengths. Some diamonds are transparent in the ultraviolet region, the visible region, and most of the far infrared region (O.22-2.5 μm).
The superior or specific properties and properties of the above superhard materials determine their broad use.
Compared with natural diamond (ND), artificial polycrystalline diamond (PCD) has a slightly lower hardness, Young's modulus and thermal conductivity, and slightly higher fracture toughness and thermal expansion. The various properties of artificial CVD diamond are between ND and PCD, closer to natural diamond. For example, natural diamond has a hardness of 10,000 HV, a PCD of about 8000 HV, and a CVD diamond of 9000 HV.
5 Application range of superhard tool materials
Cubic boron nitride has high hardness, high thermal stability and is inert to iron-based elements, so it is most suitable for making tools for cutting the following materials:
Cutting all kinds of hardened steel, including carbon tool steel, alloy tool steel, high speed steel, bearing steel, die steel, etc.;
Cutting a variety of iron-based, nickel-based, cobalt-based and other thermal spray (welded) parts.
Diamond has higher hardness and other excellent properties. It produces a wide range of tools and can process a variety of difficult-to-machine materials and non-difficult materials.
For non-ferrous metals, mainly for copper, aluminum and their alloys, ultra-precision machining; because diamond tools, especially natural diamond tools, the cutting edge can be sharply sharpened, and the nano-scale blunt radius can be ground;
Cutting pure tungsten, pure molybdenum;
Cutting engineering ceramics, cemented carbide, industrial glass;
Cutting graphite, various plastics;
Cutting a variety of composite materials, including metal-based and non-metal-based, fiber-reinforced and particle-reinforced;
Various medical device tools used in dentistry and orthopedics;
Used in a variety of woodworking tools and stone processing tools;
......
Diamond and cubic boron nitride single crystal powders are widely used in the production of abrasives, abrasives, abrasives, abrasive cloths, and sandpaper.
Diamond is also widely used in the production of wire drawing dies, grinding wheel modifiers and drilling drill bits in the petroleum and geology sectors. Also used in a variety of wear parts.
Most of the difficult-to-machine materials that can be cut with diamond tools, such as cemented carbide, ceramics, glass, composites, etc., can also be used for cubic boron nitride tools, but the service life of cubic boron nitride tools is generally lower than that of diamond tools. Diamond tools cannot process iron-based materials.
Yangzhou Chengde is a Jointer venture company with American top Aerospace and Energy products conglomerate PCC Group, fully integrated with PCC on technology and management. We can produce all the boiler pipes according to the ASME SA335, ASTM A335 and EN10216 standards, such as the P11 steel pipe, P12 steel pipe, P22 steel pipe, P91 steel pipe, P92 steel pipe, P5 steel pipe, P9 steel pipe, P36 steel pipe, 10CrMo5-5 steel pipe, 10CrMo9-10 steel pipe, 13CrMo4-5 steel pipe, 15NiCuMoNb5-6-4 steel pipe, X10CrMoVNb9-1 steel pipe and X10CrWMoVNb9-2 steel pipe
In the year of 2015, we win the first prize of National Science and Technology Progress Award by the program of [The innovative research & development, and application of steel pipes used in 600 ℃ Ultra-super critical coal power generation unit".
Yangzhou Chengde is continuously strengthening the technical innovation, together with Bao steel and other companies. Yangzhou Chengde has spent 10 years on the R&D of the steel pipe used in 600 ℃ Ultra-super critical coal power generation unit and achieved the tremendous success on realizing the manufacture of such high-end seamless steel pipe from zero to the advance level, which has filled up the vacancy in China and broken up the foreign technological monopoly. The steel pipe manufacturing technology of China has leaped to the international advanced level and further confirmed the leading position of Chinese companies in researching and making high-end special steel pipes.
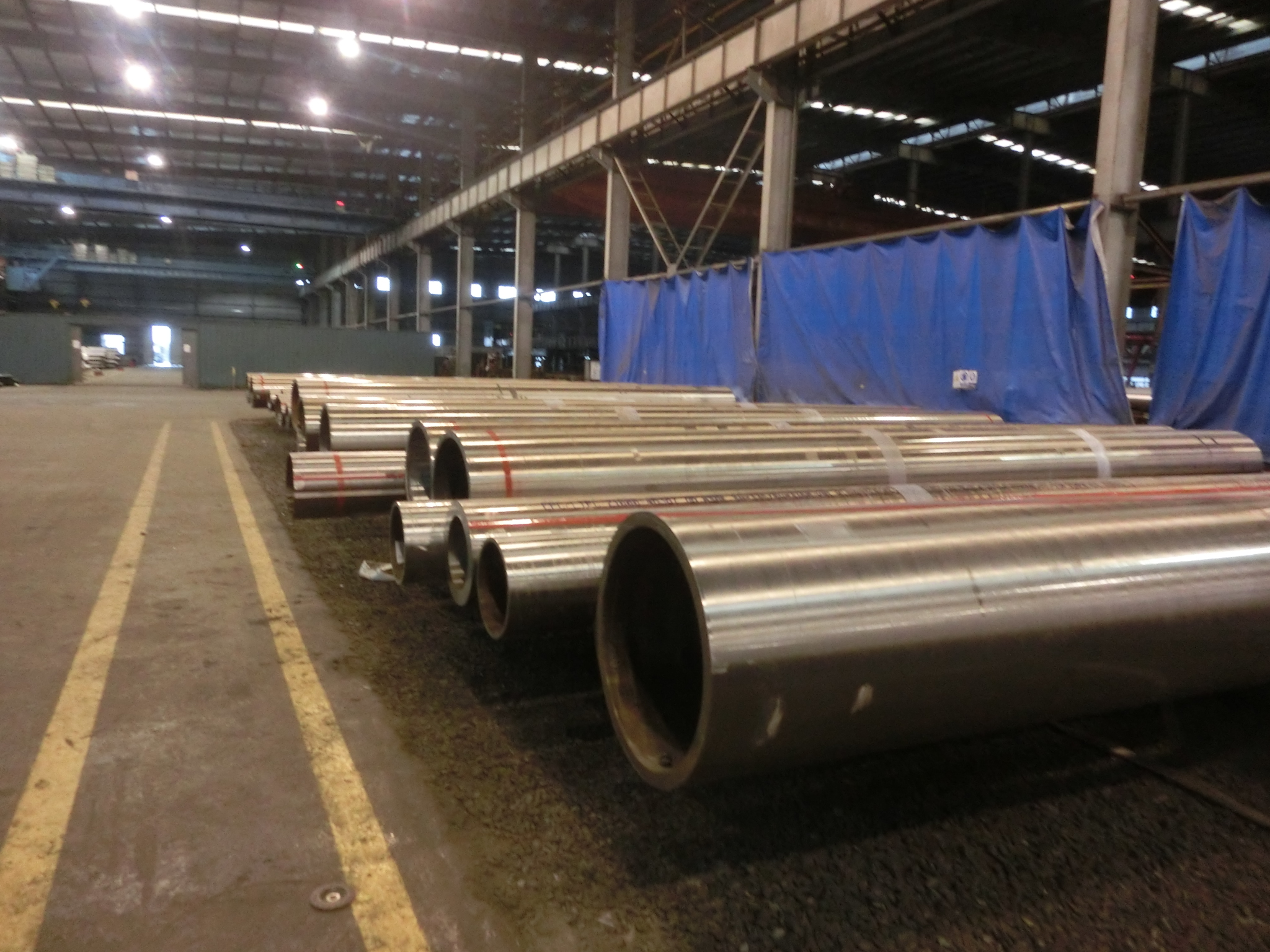
Boiler Pipe,Thermal Power Pipe,P9 Pipe,P36 Pipe
YANGZHOU CHENGDE STEEL PIPE CO.,LTD , http://www.chengdepipe.com