Liu Zhigang 1
Jiangxi Copper Group Guixi Smelter, Guixi 335424, Jiangxi, China
Jiangxi Copper Group Guixi Smelter, Guixi 335424, Jiangxi, China
[ Abstract]
This article describes the Guixi smelter through the independent research and development will be imported M28 disc casting machine system successfully transformed, using a generic replacement of spare parts for professional spare parts programmatically, breaking the foreign monopoly of technology, the system running smoothly, reliable, with good promotion value .
This article tells that through a series of independent researches and developments Guixi smelter have succeeding the import M28 disc casting machinery .We redesigned the operating system to make the machinery work more stably and rusty .And because of this transformation ,We made it possible that We can use the general spare parts to replace the professional spare parts. Due to the successful development, we have broke the foreign technology monopoly .This transformation has good promotional value.
[ Key words] M28 disc casting machine; copper anode plate ; PLC technology; independent research and development
CLC number:
1 Introduction
Guixi Smelter Melting Workshop One System Anode Furnace The 28-die disc casting machine is a second-stage equipment. It was imported from abroad in 1995 and has an 85-ton per hour casting capacity. The system is a double-bundle casting and is an advanced automatic casting system. The cast anode plate is accurate and has good shape and surface conditions.
2. Reasons for upgrading However, due to the long period of equipment use, all special electrical spare parts have been discontinued. The M28 disc casting machine is produced by Outokumpu, Finland. For commercial reasons, the company's controllers, inverters and other electrical spare parts are implemented using proprietary hardware. They are technical monopoly equipment and can only be used in the event of a failure. Procurement, please solve it with foreign experts. With the increase of the service life, Outokumpu's system has been upgraded several times, all of its individual components have ceased production, and the market has no identical models or alternative products, which has brought a huge passive situation to maintenance. Failure to take appropriate response measures in time will inevitably result in a loss of control, posing a threat to the continuity and stability of production. According to the experts of Outokumpu, we must replace and upgrade the entire electrical control system, and the upgrade cost is up to 2 million yuan (RMB). Even with the upgrade, future equipment maintenance and spare parts purchase are completely subject to the company.
Based on the above situation, in 2010 Guixi Smelter set up a research and development group to carry out the localization transformation of the electrical control system, replace the proprietary equipment with a universal device, and break the company's technical monopoly. Through in-depth research and analysis of the original system, we adopted general-purpose devices such as programmable logic controllers (PLCs) and domestic electronic scales on the market. Through software programming, we not only completely simulated and implemented the functions of the original controllers, but also increased the production shop customization capabilities. It is very practical.
3 Process and equipment composition
3.1 Anode casting process The main function of the disc casting machine in the copper smelting process is to cast the anode furnace molten copper into an anode plate of uniform weight and then send it to the electrolysis plant for electrolysis. As the quality of the anode plate directly affects the quality of the electrolytic copper, casting control is very important. [1]
The liquid copper flows out of the copper outlet of the anode furnace and flows into the tundish after passing through the flow cell. When a certain amount of copper liquid is reached in the tundish, it begins to inject the copper liquid into the casting package placed on the electronic scale when the liquid is poured. When the copper water reaches the set weight, the tundish automatically returns and begins to inject the copper liquid into the other side of the casting bag. After the blank mold on the disk reaches the casting position, the casting package starts to cast copper liquid into the copper mold according to a setting procedure. When the injection volume reaches the single weight of the set anode plate, the casting package stops casting. Then, the disc rotates, and the copper mold filled with copper liquid enters the spray cooling zone for cooling, and the tundish and the casting bag repeat the previous action. In the spray cooling zone, the anode plates that have not yet solidified are forced to cool and the copper molds are evenly cooled. After that, the anode plate is turned to the pre-pushing position, the jacking cylinder moves, and the anode plate is lifted. The anode plate is continuously transferred to the extractor position, the anode plate is lifted again, and the extractor takes the anode plate out of the disk and transports it to a cooling water tank for further cooling. After the anode plate in the water tank reaches a set amount, the chain conveyor in the cooling water tank sends the whole anode plate to the rear end of the cooling water tank, and the stacking plate lifter lifts the whole anode plate and then uses a forklift. Fork shipped to the yard. After the anode plate in the mold is removed, the mold continues to transfer to the spray zone. The spray device sprays the mold with a layer of release agent and then enters the casting site for casting. This is a cyclical operation until the end of casting.
3.2 Equipment Composition (1) A casting system: 1 tundish, 2 casting packages, 2 electronic scales.
(2) A disc system: 28 molds, 1 disc, 1 drive mechanism.
(3) Extraction system: 3 sets of extractors and 3 sinks.
(4) Cooling system: 12 spray hoods and 24 spray valves.
(5) Control system: 1 PLC and 2 single board computers.
(6) PC monitoring system: 1 set of IPC and 2 touch screens.
3.3 Technical parameters (1) Casting time 12 to 14 seconds (2) Measurement accuracy of electronic scale <±1%
(3) Casting speed 75-85 tons/hour (4) Disc diameter 16600mm
(5) Weight of disc 200 tons (6) Number of molds 28 (7) Physical specification pass rate requirement 98% or more
2 The composition and problems of the original control system
2.1 The composition of the original control system The original control system consists of three controllers, a set of Omron CV500 series PLCs and two sets of Motorola single-board computers. The PLC controls all parts except casting. A set of single board machines controls the casting of a casting package. The PLC's operation signal is monitored by a host computer. The PC software is version 7.11 INTOUCH and communicates through the serial port. The computer of the upper computer is an ordinary computer. The display is a CRT monitor, and the input is realized by a keyboard and a mouse. Each single board computer is connected to a proface touch screen and communicates via RS485. The proface touch screen is used to adjust casting parameters and display weight information.
2.1 Problems with the original control system PC software version 7.11 INTOUCH and Omron CV500 eliminated the product, running slowly and the market difficult to buy spare parts.
The upper monitor displays a 12-inch CRT monitor, which has a large volume, a small display interface, and an unclear interface.
The PC of the upper computer is a PC computer produced in the 1990s, which is slow in operation, generates a lot of heat, and has a high failure rate. With the mouse and keyboard, operation is troublesome.
Casting single-board computer is a controller that realizes quantitative casting. It is a proprietary hardware and belongs to a technical monopoly equipment. It does not provide external control programs. In the event of a failure, it can only be purchased from the original manufacturer. Foreign experts are required to solve it or complete the replacement. The cost is extremely high and the production has been suspended and it has to be upgraded.
Casting electronic scales are devices that measure the weight of copper water to achieve quantitative casting. The scale body adopts single sensor and lever structure. The structure is complex, the mechanical precision is high, the field environment is demanding, and the failure rate is high. The signal processing device is a single circuit board. The school scale relies on changing the connection mode of the circuit board jumper for several times. The process of the comparison scale is complicated, the operation time is long, the labor intensity is high, and it cannot be monitored online.
3 Technical Principles and Schemes for Localization of Control Systems
3.1 PC software upgrade The original PC software is 7.11 version INTOUCH, use the latest version of the 10.1 version INTOUCH software. Use version 10.1 software to open 7.11 version of the program, the system will be directly converted to 10.1 program, after the conversion is complete, you can directly open and run.
The communication mode was changed from serial port mode to Ethernet communication mode. Intouch Communication Software IOSEVER changed to DASEVER. The name of the project under the original tagname dictionary is modified according to the requirements of the DASEVER document. The communication protocol of the access name remodels the DASEVER protocol. Through the router connection, the system forms an Ethernet network, set up their own IP address, intouch can communicate with the PLC.
3.2 Upgrade of PLC The original system is CV500 series PLC. The program is directly converted into CS1 series PLC program by CX-programmer software. Since there are many inconsistencies in the usage of the two series of PLCs, there will be a warning message after the program is converted. According to the usage and process requirements of the two series, the alarm program is deleted and re-programmed to achieve the original function.
On the hardware, the CV500 series PLC models are replaced with the CS1 series PLC CPU models. The number of input and output points on the module is exactly the same. This ensures that the wiring method does not require major changes and the address does not need to be changed. Replace the full set of PLC components. The original Omron CV500 series PLC was abolished and used Omron's highest series of CS1 series PLCs: the CPU was CS1H-67H, the input module was CS1W-ID261 4, the output module was CS1W-OD261 2, and the analog input module was AD041 1. The analog output module is DA041-V1 1 block. Replace all obsolete components. See Table 1, PLC hardware comparison table.
CPU | Digital input module | Digital output module | Analog input module | Analog output module | Communication module | |
Original hardware configuration | CV500 | C500-ID213 | C500-OD213 | no | no | no |
Hardware configuration | CS1H-67H | CS1W -ID261 | CS1W -OD261 | CS1W-DA041 | CS1W-DA041 | CS1W-ETN21 |
The original quantitative casting system (electronic scale, single board computer electrical control system, report printing system, host monitoring operating system and hydraulic components) was introduced by Outokumpu. Without considering the changes of electrical components, hydraulic components and other mechanical structures in the site, the original single board computer electrical control system is abandoned and the overall logic is packaged in the PLC. The electronic scale strain resistor 3T sensor 4-20mv voltage is measured by professional electronic scales. The output 4-20mA standard signal is provided to the PLC.
Abolished 2 Proface casting touch screens, configured new IPCs instead of touch screens, and programmed Intouch to realize parameter setting and monitoring of casting. Each casting unit has an independent monitoring function, using the INTOUCH program to create a picture that is exactly the same as the original touch screen, and monitors the data of each anode plate.
Turn complicated hardware circuits into program control. Completely get rid of the passiveness caused by the technical blockade of foreign single-board computers. A 25,698 PLC control program was programmed to realize the dynamic control of the casting system by the PLC program. Due to the high temperature of 1120°C copper water, an anode plate with a weight of 398kg is to be cast, and the weight deviation of the anode plate is required to be not more than 1%. The plate surface is flat and there is no flash burr. This requires extremely high control accuracy, the system can automatically complete the automatic adjustment in various environments.
Casting speed is achieved by tilting the angle of the casting oil cylinder, and the tilting of the casting oil cylinder is controlled by the servo valve voltage V. The intouch touch screen is set with the casting valve servo valve voltage V. PLC automatically adjusts the proportional valve voltage according to the weight of the anode plate casting. When the copper water flow is within a certain weight range, the servo valve voltage of the weight range is appropriately reduced. small. Conversely, when the flow rate of copper water is small, the servo valve voltage increases appropriately. After adjustment, the system will run according to the set curve each time. Figure 1, the relationship between the servo valve voltage and the weight of the anode plate changes. The casting package needs to be started quickly, the servo valve voltage is high and the tilting speed is faster. When the copper water flows out, the weight of the anode plate increases, the system automatically reduces the servo valve voltage, and the tilting speed gradually decreases. When the anode plate is increased to about 200Kg, the tilting speed is stabilized in an extremely small state. Until the weight of the anode plate reaches 360kg or so, the casting package gradually returns, and the remaining amount of 38Kg is replenished by the remaining amount of copper water. After the flow is terminated, the weight of the anode plate just reaches the standard weight of 398Kg. The servo valve voltage controls the flow of copper water. Copper water flow directly affects the anode plate physical specification qualification rate. The flow of copper water must be controlled in a balanced and steady state. The flow rate is large and flashes and burrs are easily generated. The flow rate is small and cold copper bonding is likely to occur. Through the dynamic control of the PLC program, the servo valve automatically adjusts the flow, achieves the balance and stability of the flow, and ensures the pass rate and weight standard of the physical specification. This is the most critical and core technology of the system. As shown in Figure 2, the flow of copper water is a function of time.
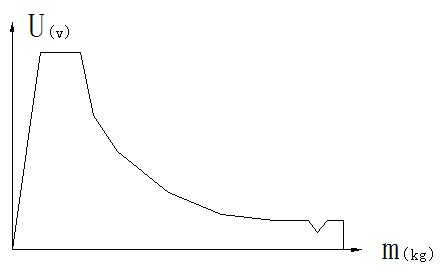
Figure 1. Relationship between servo valve voltage and anode plate weight
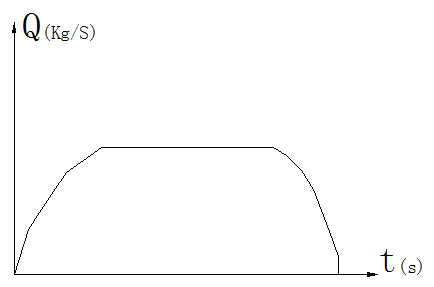
Figure 2. Relationship between copper water flow and time
3.4 Upgrading of Casting Electronic Scales Quantitative casting devices can be simply divided into weighing devices and casting devices. The weighing device is an electronic scale. The weight of the entire casting package is applied to the scale through three points and then transmitted to the sensor via the support link. The entire casting system is controlled by a hydraulic system [1].
The weighed object is placed on the weighing platform, under the action of gravity, a 3T load cell strain gauge of the electronic scale is deformed, so that the resistance strain gauge bridge pasted on the elastic body stress beam loses balance, output and weight The data is proportional to the voltage signal. The signal enters the weighing signal processing circuit board. After being linearly amplified, the weight signal is processed by the single board computer and the weight data is directly displayed on the weighing instrument and stored. The electronic scale has a measurement accuracy of 0.01kg. The scale body adopts a single sensor, a lever mechanism, and the structure is complex. It is impossible to produce electronic scales of this structure type in China. According to the process requirements, we independently developed an electronic scale with exactly the same dimensions and functions. The structure adopts a four-sensor method, and the weight of the scale body is supported on four sensors, and the structure is relatively simple.
The original weighing signal processing circuit board (Weight transmitter pr 1590/00) also has no relevant spare parts selected, and the use of domestically-made special electronic scale instruments is used instead. The sensor cable is connected to the electronic scale instrument, and the electronic scale instrument outputs the standard 4-20mA. Signal processing is achieved. The scale process is greatly simplified. Zero and full scale weights are calibrated on the operator interface to complete the calibration of the electronic scale. The operation process takes only 5 minutes and is quick and intuitive.
After receiving the analog signal from the electronic scale, the PLC dynamically calculates the casting speed and automatically controls the weight of each anode plate to finally realize quantitative casting.
4 The logical relationship between the old and new system hardware is compared with the three control units of the original system (1 PLC + 2 cast single board computers) into a control unit (1 PLC). The control program is centralized in one PLC and completely replaces the three control unit modes.
The monitoring system consists of three man-machine interfaces (1 intouch man-machine interface + 2 proface touch screens) and 2 man-machine interfaces (2 intouch man-machine interfaces). The hardware structure is greatly simplified.
The complex multiple RS232 and RS485 serial port communication becomes an Ethernet communication, the communication speed is improved, and the communication unit is simplified. See Figure 2, Figure 3.
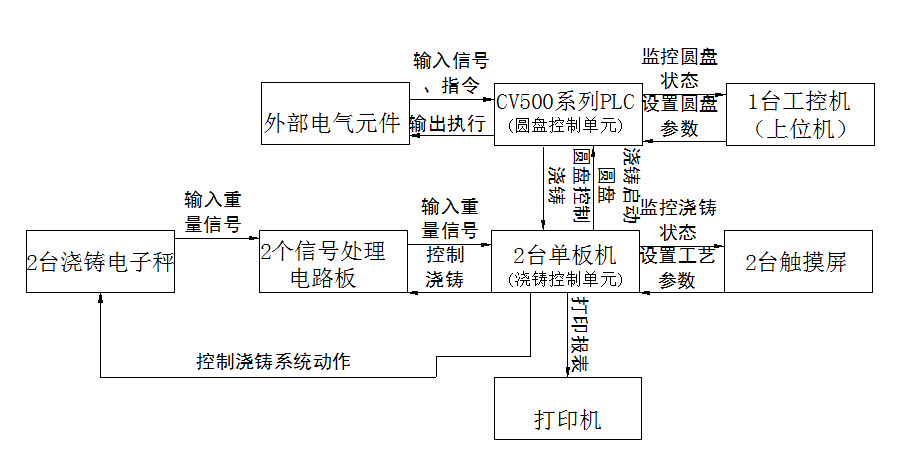
Figure 3, the original control system hardware logic relationship
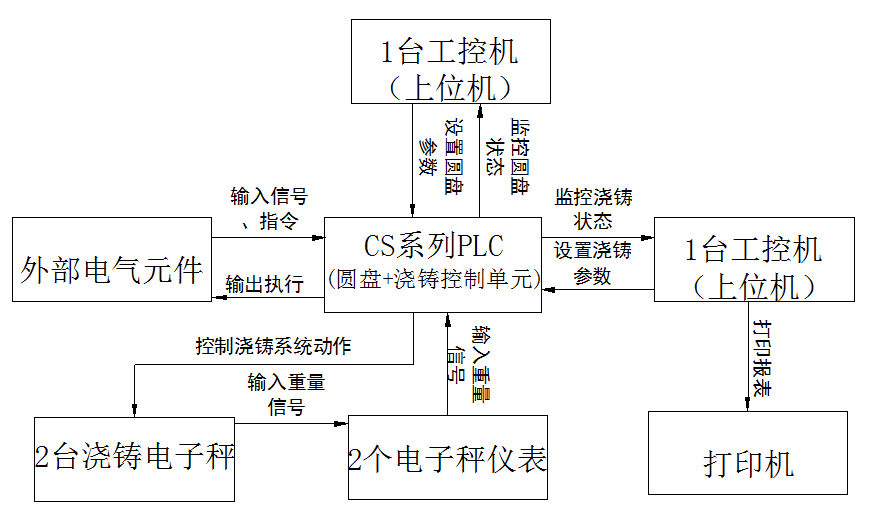
Figure 4. The current hardware relationship of the control system
5 Comparison of Operation of the Old and New Systems Although the hardware and software are completely different in the new control system, they are completely in accordance with the original model and are simulated and developed. All process operating habits are consistent with the original system. Operators can perform production operations without training. The previous keyboard operation became a touch operation, and the operation was faster than before.
6, transformation effect
6.1 The first time after the transformation of the new system to produce copper, it will be able to cast qualified anode plates.
6.2 99% of the anode plate weight deviation is within +/-1Kg, 100% anode plate weight is within +/-3Kg, the anode plate surface is smooth, no flash burr, the physical specification pass rate of 98.5%, more than before 0.5%.
6.3 The simplification of the hardware, the failure rate is reduced by more than 50%, and the failure no longer depends on foreign experts. Any failure can be quickly and autonomously eliminated, and the troubleshooting time is greatly reduced.
6.4 The system upgrades, autonomously mastered the core technology, got rid of the foreign technology blockade, spare parts procurement is fast, and the cost is low, saving 1 million yuan in spare parts costs every year.
6.5 System upgrades The system's casting speed has been improved. The casting speed has been increased by 5 tons/hour and the maximum is 90 tons/hour.
7 Conclusion The independent research and development of the system was upgraded and the core technology was under control. Simple equipment maintenance, low failure rate, and easier operation. The retrofitted system has been in operation since November 2011. In a year and a half, the operation has been stable and reliable. There has never been a single device failure that caused downtime and terminated the casting phenomenon. The success of the domestic transformation of the M28 disc not only broke the monopoly of foreign companies on the M28 disc casting machine technology, saved system upgrades and maintenance costs, but also enhanced the technical equipment capabilities of our plant's metallurgical equipment. In the upgrading of similar products at home and abroad, it has promotion value.
references:
[1] Huang Qizhi. Discussion on improving the quality of anode copper plate in disc casting machine [J]. Non-ferrous smelting. August 2002, No. 4: 42-44;
[2] Fang Yong. Design characteristics and maintenance of disc casting machine. Copper Engineering [J]. 2004, NO.3 29-31;
· Basin Mixer can follow your bathroom designs. Colors can be customized colors like golden, bronze, brush nickel, antique copper, Oil rubbed bronze, rosy brown, baking varnish, etc. Concealed wall mounted basin mixer, Vessel Sink Mixer, polished surfaces and various shapes make the washroom perfect for modern environments.
Basin Mixer
Single Lever Basin Tap,Single Hole Basin Tap,Single Cold Pillar Taps,Lift Up Lever Cold Taps
SHENZHEN KING OF SUN INDUSTRY CO.,LTD , https://www.handyfaucet.com