Home>Bearing knowledge>Delcam software in the production of car cover parts mold (on) |
Application of Delcam Software in the Production of Car Covering Moulds (Part I)
/*250*250 was created on 2017/12/25*/ var cpro_id = 'u3171089'; |
Second, the three-dimensional external Jetta car all sides of the imitation mold cavity some of us to use reverse engineering methods to make it; to PowerSHAPE process to make up. DELCAM company's software SHASHA software intelligentSHA and intelligent toolbar; Great locality has our operation; and its strong surface shape and surface modification function; especially suitable for the process to make up for the depiction.
Third, CNC machining The CAD model generated in the PowerSHAPE module is directly transmitted to PowerMILL; according to the characteristics of the side wall model; the NC machining process road is proposed; the process is as follows:
(1) Roughing because of the large amount of castings; roughing we use Ф50R6 round end milling cutter for layering processing. PowerMILL's layered processing can intelligently think about the casting amount of blank; optimize the tool path. Racing line roughing is PowerMILL's unique machining strategy; it maximizes the rounded corners to smooth the sharp corners of the tool path; and selects the selected cycloidal machining in the recessed area of ​​the tool overload; these fit the high speed The need for processing. After the practice of the test; the use of layered processing to save a lot of time compared to the parallel processing selected by us.
(2) Process after roughing The process of root clearing is to remove the data that cannot be processed at the concave corner of the rough or semi-finished part; thus the processing capacity of the next process is more uniform; The processing speed of the process; the intention to reach the progressive power. Because we have used large tools for roughing; there are still many residual margins in the groove area; therefore we decided to do a process after roughing. Because we need to use Ф20 ball-end knives during finishing; therefore, we also use Ф20 ball-end knives in this process. The selected processing strategy is PowerMILL's layered root processing based on common knowledge of blanks; Intelligently identify the unprocessed area after the previous processing; think about the residual margin left after the last processing; optimize the tool path of the remaining area;
(3) Semi-finishing Because roughing is only to remove too much margin; there is no need for appearance quality and precision; therefore, the selected layer height is large; after processing, a step-like margin is left on the exterior of the part. This appearance; leaving a uniform machining allowance for finishing; ensuring smooth tool force during finishing; stable cutting conditions; semi-finishing of parts is required. Semi-finishing we use PowerMILL to process according to the characteristics of the model. The shoal processing method; we choose the ball cutter of Ф30; with the 45° angle as the boundary; the PowerMILL shoal method will intelligently divide the model into the flat area and the steep area; the flat area we choose parallel processing; the arc connection, the steep area We use contour processing; we use rounded smoothing at the sharp corners of the parallel and contoured tool paths; and cooperate with the spiral feed method; these methods also meet the needs of high-speed machining; together Greatly improved our processing power and extended our tool life. This method of processing according to the model avoids parallel processing. Steep region of the tool carrier is too large; easy to form a broken tool; processing is a very good way.
(4) The process before the finishing process uses the pen-type rooting in the PowerMILL finishing strategy to remove the residual margin that cannot be processed at the concave corner; this greatly improves the finishing power.
Recommend to friends comments close window
Bearing related knowledge |
The classification of ceramic bearings, the diagnosis of rolling bearings, the diagnosis of the oscillation analysis of several improvements in the strength of imported bearings, the newest learning of the bearing shortcuts list, the first move, how do you understand the bearing? |
This article links to http://
Please indicate the bearing network http://
Previous:How to choose the appropriate type of rolling bearing Next:The bearing of diesel engine hydraulic transmission system
These diamond drill bits are made of industrial grade carbon steel with nickel-plated coated body to resist corrosion. A thicken diamond coating on the tops offers superior cutting strength for maximum drilling outcomes.
Each diamond Hole Saw has a smooth and exact finish that lower the incision resistance and drill pressure, increases the sharpness, and effectiveness of water lubrication. Excellent for making clean and precise holes on glass or ceramic and considerably extending Drill Bit life.
Perfect for drilling glass, tile, porcelain tile, ceramic tile, brick, and stone
These glass hole saw set along the drill bit facilitate the entrance of cooling water and escape of chips and other particles from drilling. Makes the drilling process easier.
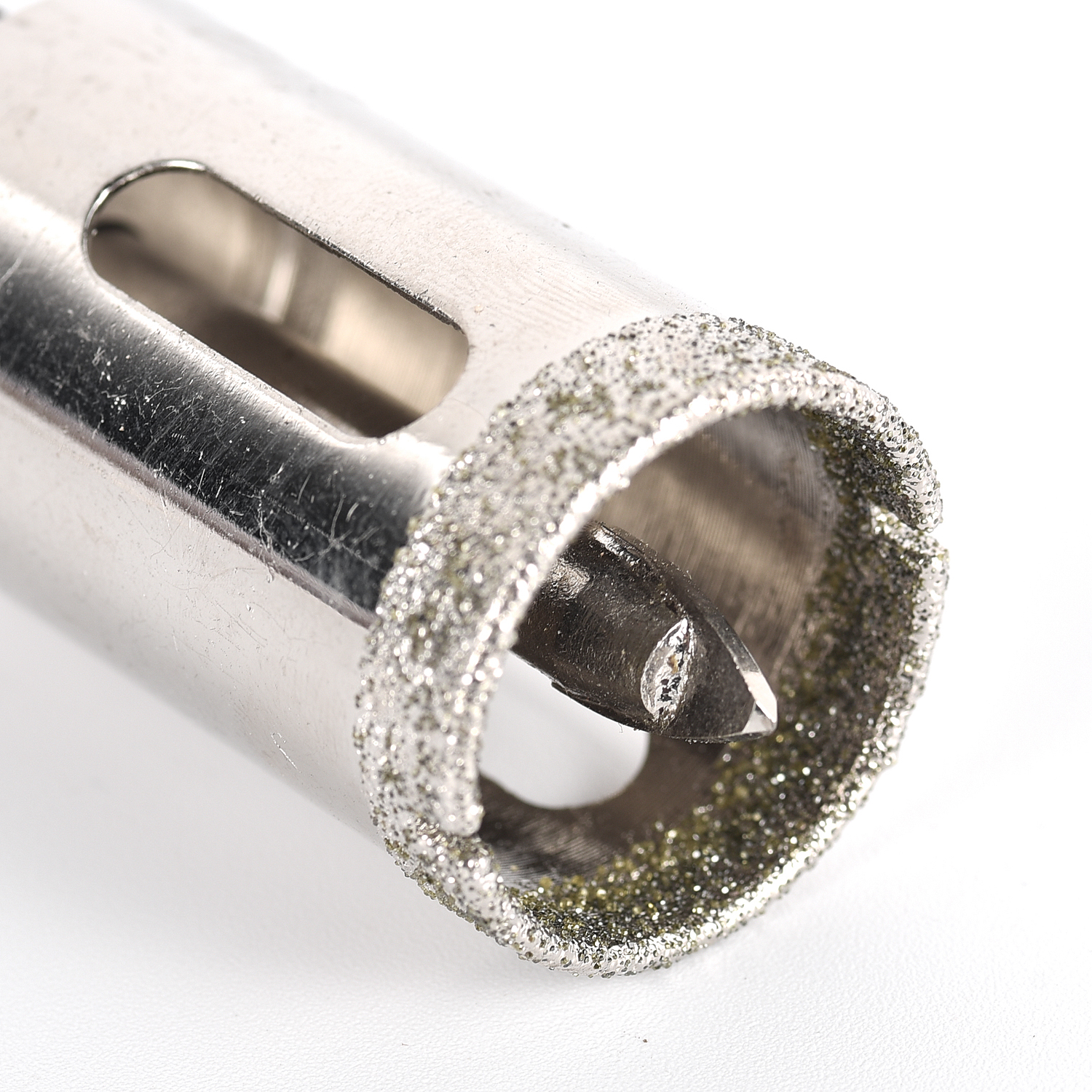
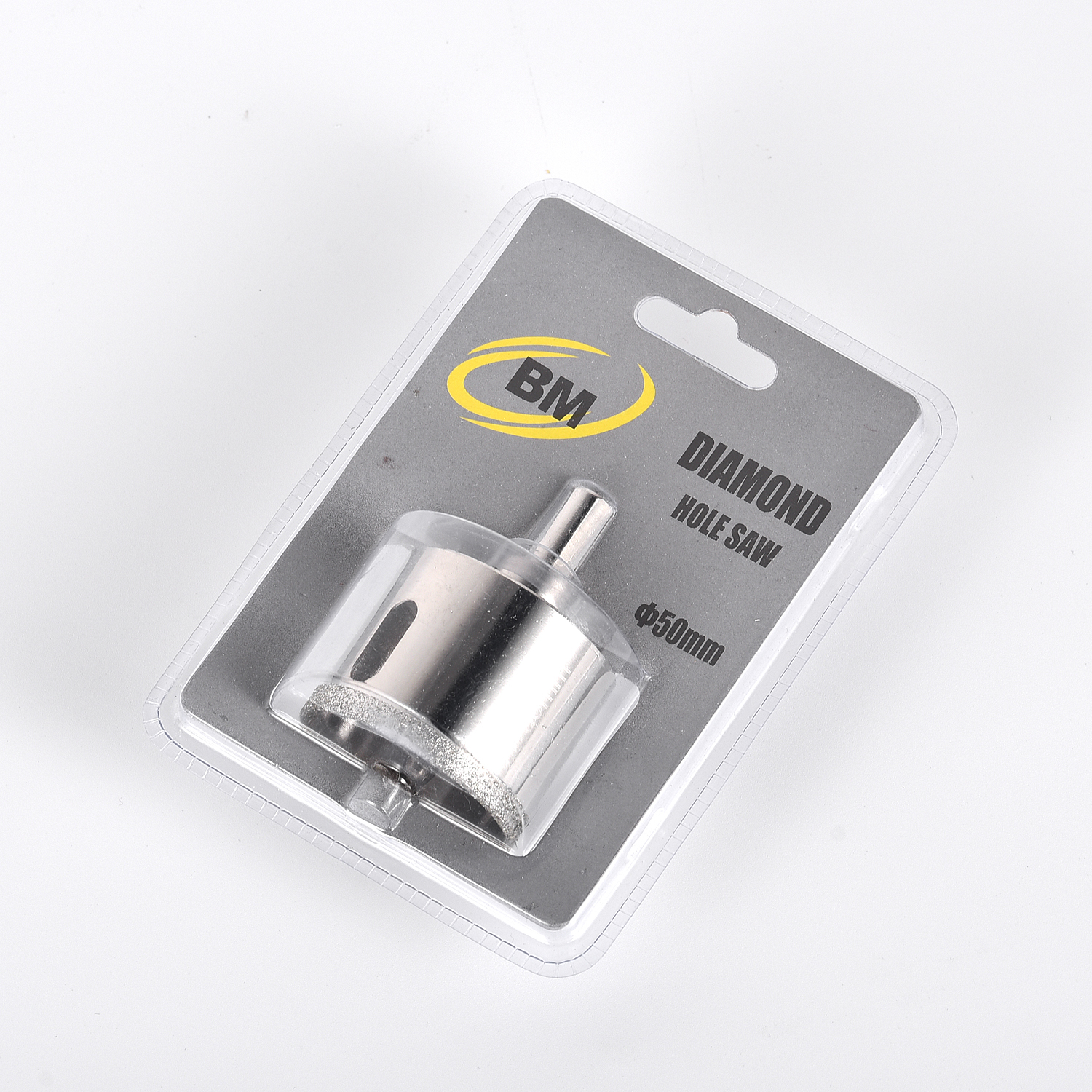
diamond hole saw,hole saw,diamond hole cutter granite,diamond hole saw at harbor freight
Behappy Crafts (suzhou)Co.,Ltd , https://www.jshaoyue.com